From the steam-powered mills of the Industrial Revolution to the assembly lines of mass production, manufacturing has continuously evolved over the centuries. Today, a new frontier of manufacturing is emerging – the mini factory. These compact, flexible, and technologically advanced production units are revolutionizing the way products are made. In this article, we delve into the world of mini factories, exploring their benefits, applications, and the future they hold.
The Rise of Mini Factories
Mini factories represent a paradigm shift in manufacturing, driven by advancements in automation, robotics, and digital technologies. These compact production units are designed to optimize space, increase productivity, and respond quickly to changing market demands. Unlike traditional factories, which require vast amounts of space and investment, mini factories function as lean, dynamic production units.

Applications Spanning Industries
Mini factories cater to a wide range of industries, from electronics and automotive to food and textiles. They are especially suited for producing high-value goods in limited quantities, or for niche markets with specific customization requirements. Let’s explore some notable examples of mini factories across different sectors:
1. Electronics Industry
In the electronics industry, mini factories excel in producing highly specialized components such as circuit boards, sensors, and semiconductors. Utilizing advanced robotic automation and precision machinery, these mini factories can achieve unparalleled levels of accuracy and quality control.
2. 3D Printing and Additive Manufacturing
One area that has seen a significant impact from mini factories is 3D printing and additive manufacturing. These compact production units enable the rapid prototyping and production of customized parts, reducing lead times and costs. Mini factories equipped with multiple 3D printers can operate around the clock, providing on-demand production capabilities.
3. Food Industry
Mini factories in the food industry are transforming the way we think about food production. From automated bakeries to small-scale hydroponic farms, these innovative facilities ensure fresh and sustainable food production while minimizing waste. The integration of smart sensors and data analytics allows for precise control over the production process, ensuring the highest quality products.

Benefits of Mini Factories
The adoption of mini factories brings a multitude of benefits to manufacturers. Let’s delve into some key advantages:
1. Increased Efficiency and Flexibility
Mini factories maximize efficiency by optimizing space and minimizing material waste. These compact production units can be easily reconfigured to accommodate different manufacturing processes or changing product lines. This flexibility allows manufacturers to adapt swiftly to market demands, reducing downtime and improving overall productivity.
2. Cost-Effectiveness
As mini factories require smaller footprints, they are more affordable in terms of real estate, infrastructure, and energy consumption compared to traditional factories. This cost-effectiveness makes them particularly attractive to start-ups and small businesses looking to enter the market with limited resources.
3. Enhanced Quality Control
Thanks to advanced automation and integrated quality control systems, mini factories offer unparalleled precision and consistency in product manufacturing. The ability to monitor and adjust production parameters in real-time ensures that every unit produced meets the highest quality standards.
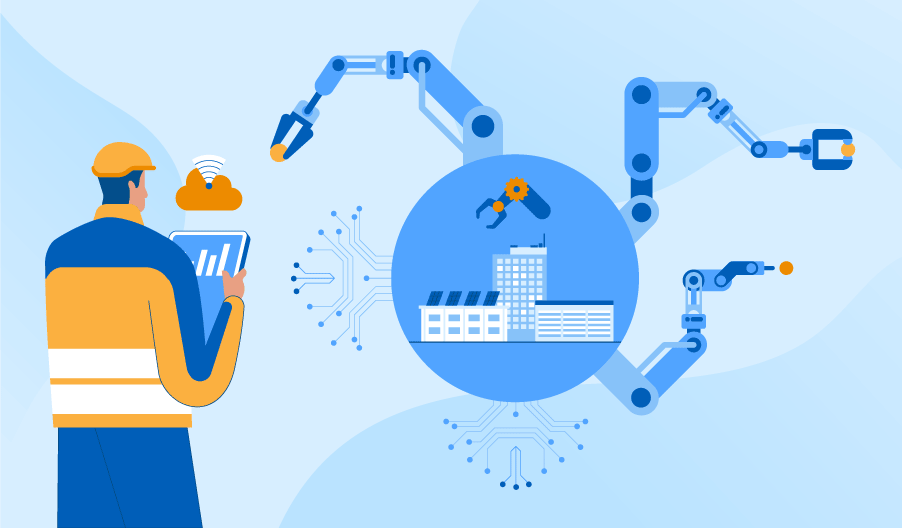
The Future of Mini Factories: Towards a Smart Manufacturing Revolution
With the rapid advancement of technologies such as artificial intelligence, the Internet of Things, and big data analytics, mini factories are evolving to become smarter and more interconnected. These developments hold immense potential for the future of manufacturing:
1. Collaborative Robotics
Mini factories are witnessing the integration of collaborative robots, or cobots, which work alongside human operators. These intelligent machines can perform repetitive tasks efficiently while maintaining a high degree of safety. The combination of human expertise and robotic efficiency revolutionizes the way products are manufactured.
2. Data\-Driven Manufacturing
The rise of mini factories in the era of Industry 4.0 brings forth the concept of data-driven manufacturing. By harnessing real-time data from sensors and machines, manufacturers can optimize production processes, identify bottlenecks, and make informed decisions. This data-driven approach enables more efficient resource allocation, predictive maintenance, and superior product customization.
3. Decentralized Production
Mini factories have the potential to decentralize production, bringing manufacturing closer to end-users. This decentralization can decrease transportation costs and reduce environmental impact. Furthermore, it allows for localized production, tailored to regional demands and cultural preferences.
Conclusion: The Mini Factory Revolution
In conclusion, mini factories represent a remarkable leap forward in manufacturing. By combining compactness, efficiency, and advanced technologies, they enable manufacturers to thrive in an increasingly competitive market. These compact powerhouses of production offer increased efficiency, flexibility, and cost-effectiveness, while enhancing quality control. As mini factories continue to evolve and embrace smart technologies, they pave the way for a new era of manufacturing, characterized by collaboration, data-driven decision-making, and decentralized production.